Made by carefully selected manufacturers according to customer needs.
All Special Order Machining Mold Bases
Faithfully reflecting the customer's particular needs.
Mold Bases for Precision Molds
Manufactured on site in a processing environmentally and friendly manner.
Large mold base and die parts
[Overseas production]
Generous support is provided until delivery.
What NIKKO KIZAI
can do for you
Our company has been working together with mold makers since our establishment.
Mold bases, which are the foundation of plastic molds, are positioned as important parts that greatly affect design, manufacturing, quality, delivery, cost, and productivity when customers are making molds. We handle a wide range of products made by carefully selected manufacturers to meet the needs of our customers.
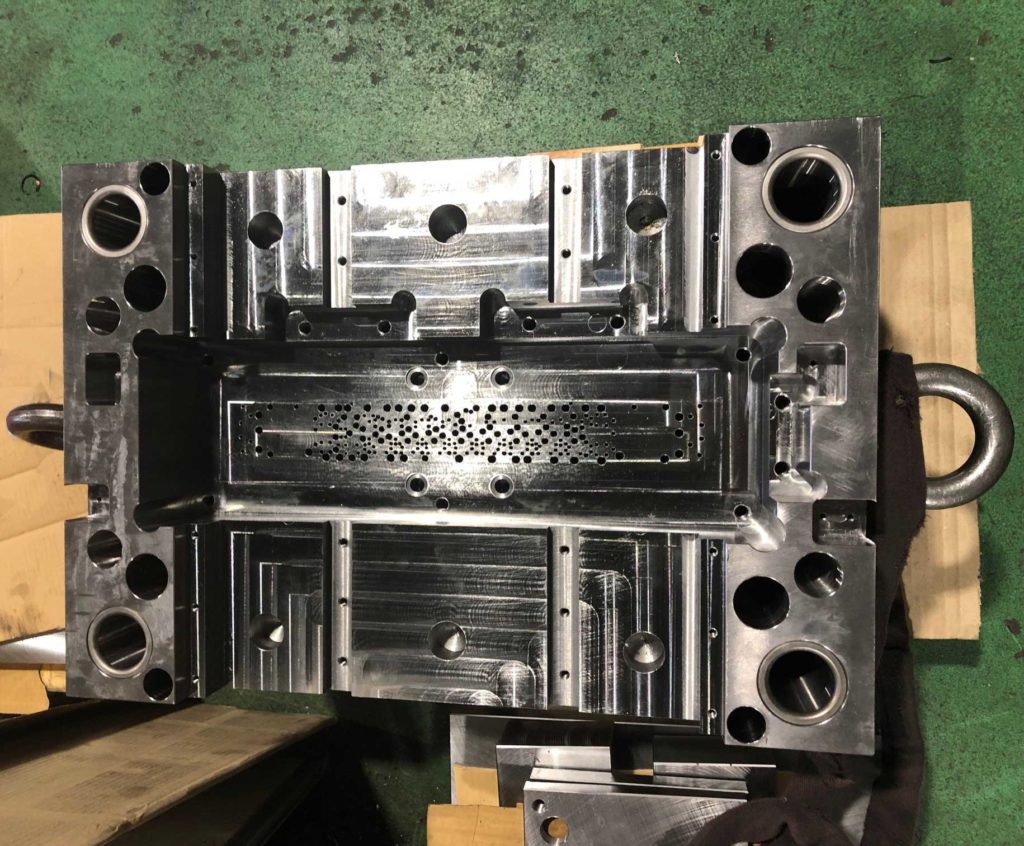
Custom-made fully machined Mold base
We provide various types of mold bases and die casting main molds, mainly custom-made fully machined mold bases. Roughing, distortion removal, and polishing from solid plate. We can achieve high precision quality, plate parallelism, hole perpendicularity, and pitch accuracy by machining guide pin holes and pockets on the same coordinate system. We can flexibly accommodate custom-made dimensions, pitches, irregular shapes, depths, multi-directional slides, material changes, and custom-ordered embedded parts. We deliver products that faithfully reflect the customer's specifications, processing methods that cannot be expressed in drawings, and particulars.
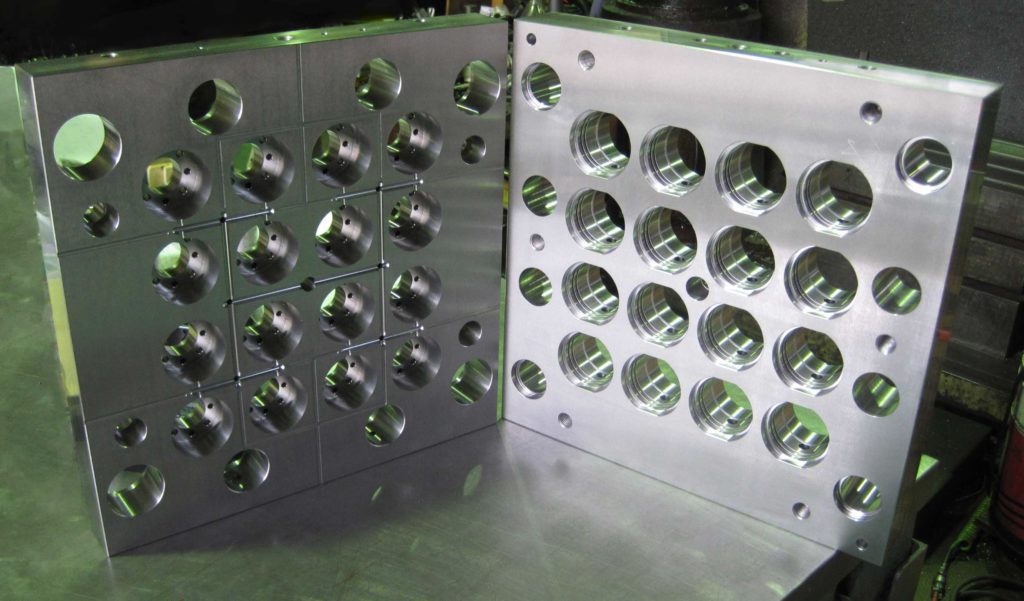
Mold Bases for Precision Molds
In order to meet the strict accuracy requirements of our customers, we manufacture our mold bases onsite, taking into consideration the machining environment. We place emphasis on boring, which is the basis of mold base production, and our high-precision guides and pocket holes have been highly evaluated for mold bases for gears, food, cosmetics, and medical applications that require hole diameter accuracy, roundness, and pitch accuracy, as well as for molds that require a large number of pieces and a large number of shots. We have a proven track record in precision mold bases used in hardened molds for connectors and other applications. This contributes to productivity improvement and total cost reduction in product mass production. We also offer wire cutting, jig grinding, slide polishing, and quenching.
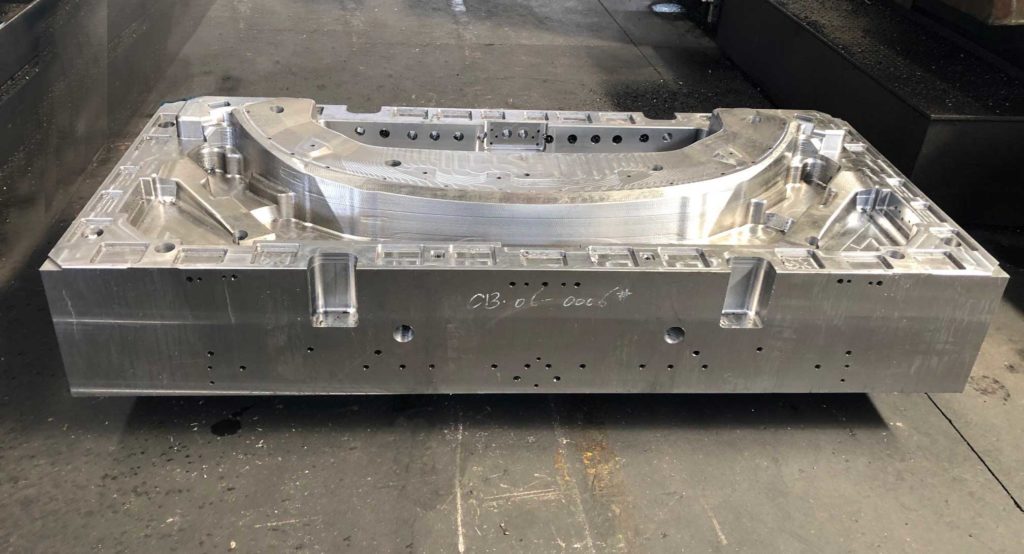
Large mold bases, mold parts [overseas production]
Utilizing our own overseas production bases, we manufacture mold bases for bumpers, instrument panels, head lamps, intake manifolds, and other large molds over 2000 mm, die-casting main molds, 3-dimensional nested molds, and parts processing at partner manufacturers selected according to the product. We provide high quality, low price, and quick delivery with our well-equipped processing facilities, inspection system, and 24-hour operation. To avoid the risk of overseas manufacturing, we report the results of measurement, inspection, and sliding confirmation before shipment, and products are shipped after confirmation by the customer. We take full responsibility for the management and handling of all processes from order receipt to drawing discussions, quality and delivery management, import operations, and post-delivery follow-up.
Process Flow
Contact Us
Please contact us first by filling out the inquiry form or calling us.
Estimate
We accept by e-mail, fax, or paper drawing.
Supported data
.dxf .dwg .x_t .step .igs
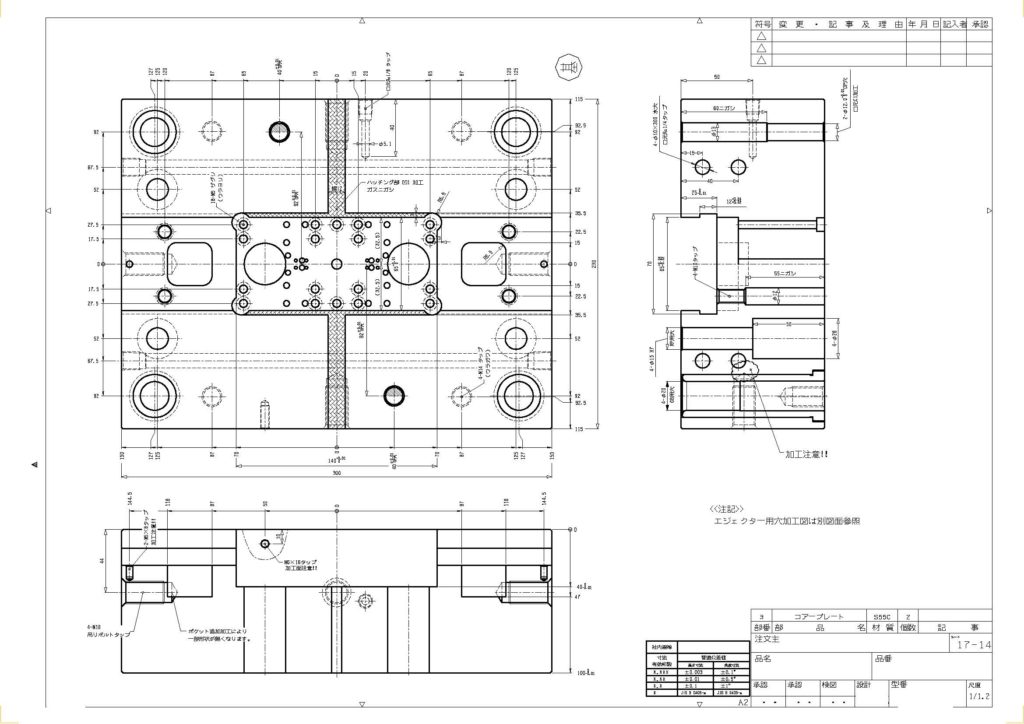
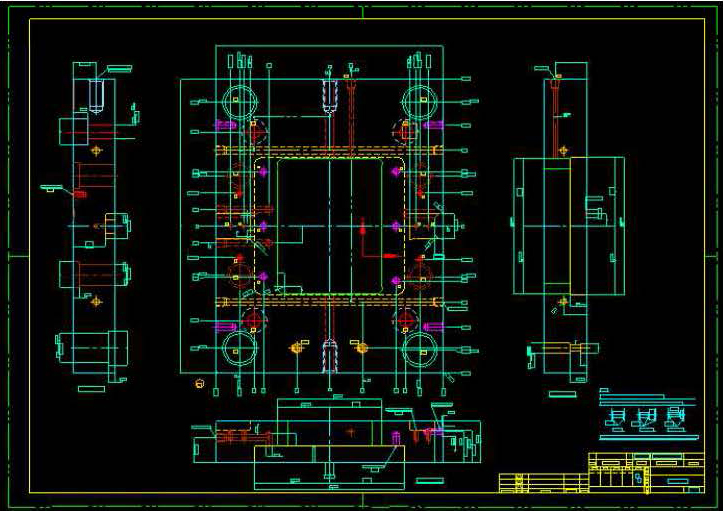
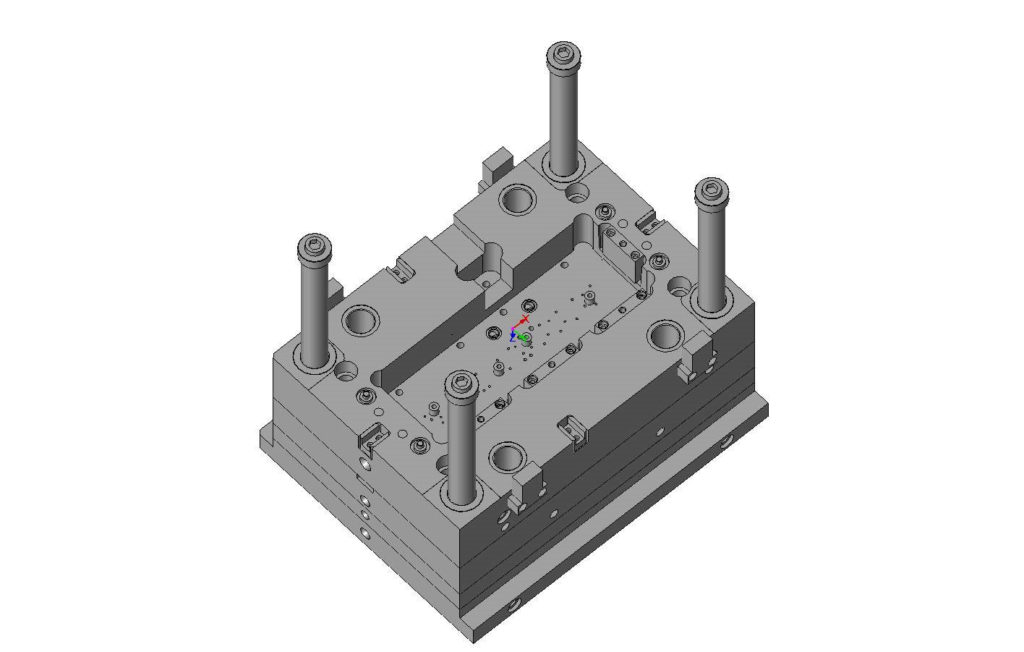
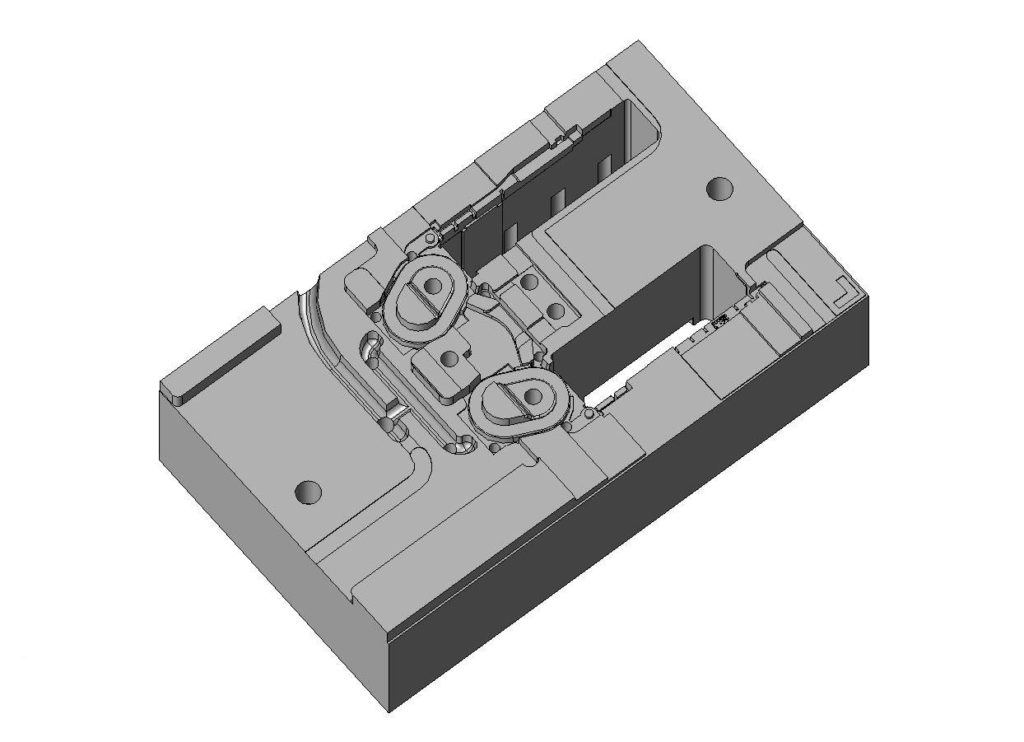
Order
We will begin to work upon receipt of a purchase order. We can also provide a quick turnaround time if you make a reservation in advance.
Appointment
We will discuss your specifications, machining methods, machining standards, dimensional tolerances, built-in parts, delivery date, etc. We can also handle 3D data only after the initial meeting.
Arrangement of materials
We arrange materials and parts. We can also handle manufacturer-specified materials, parts changes, custom-made parts, customer-supplied materials, and supplied parts.
Machining program creating
We create machining programs and drawings for each process. We flexibly respond to sudden design changes.
Processing
Measurements and inspections are conducted at each stage of the process.
Side processing | Gun drill, radial, horizontal MC |
Roughing/Hole processing | MC, side MC |
Polishing | Distortion removal, waste polishing, dimensioning, cosmetic polishing |
Finishing touches | MC, gantry MC, jig borer, wire cutter, jig grinding |
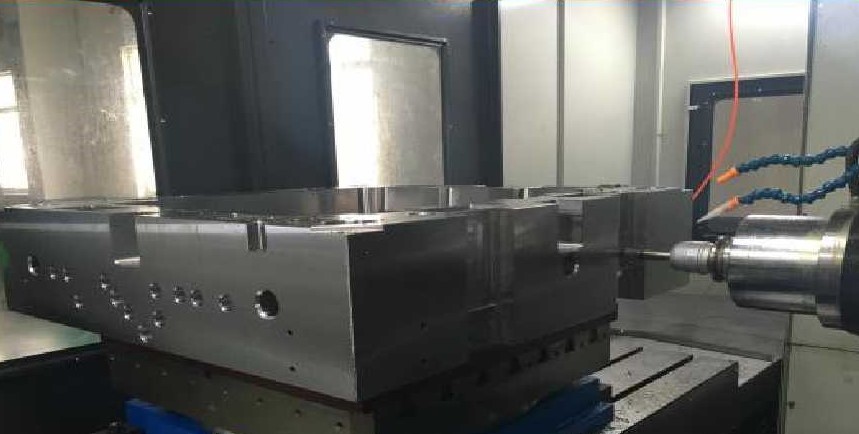
Inspection/Installation
Measurement and inspection Final confirmation.
Press fitting of parts, installation, sliding check, etc.
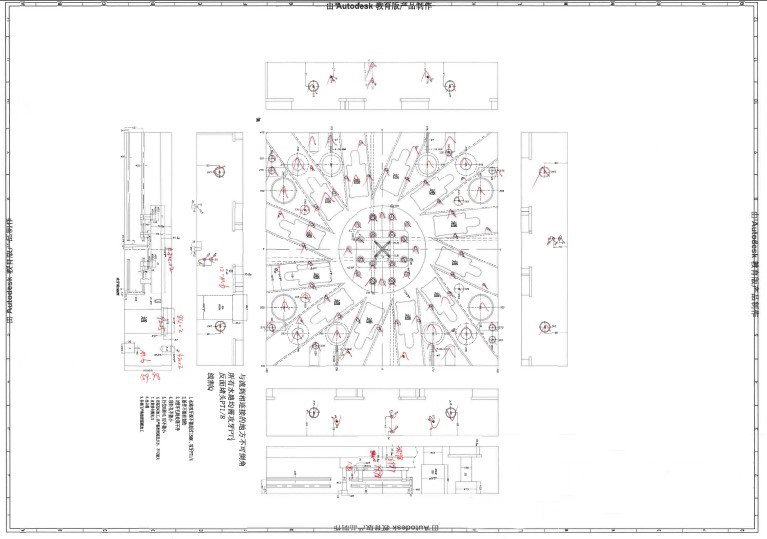
Completed
Packing and split packing are also available. About shipping and delivery Please consult with us for shipping service specification, charter service, etc.
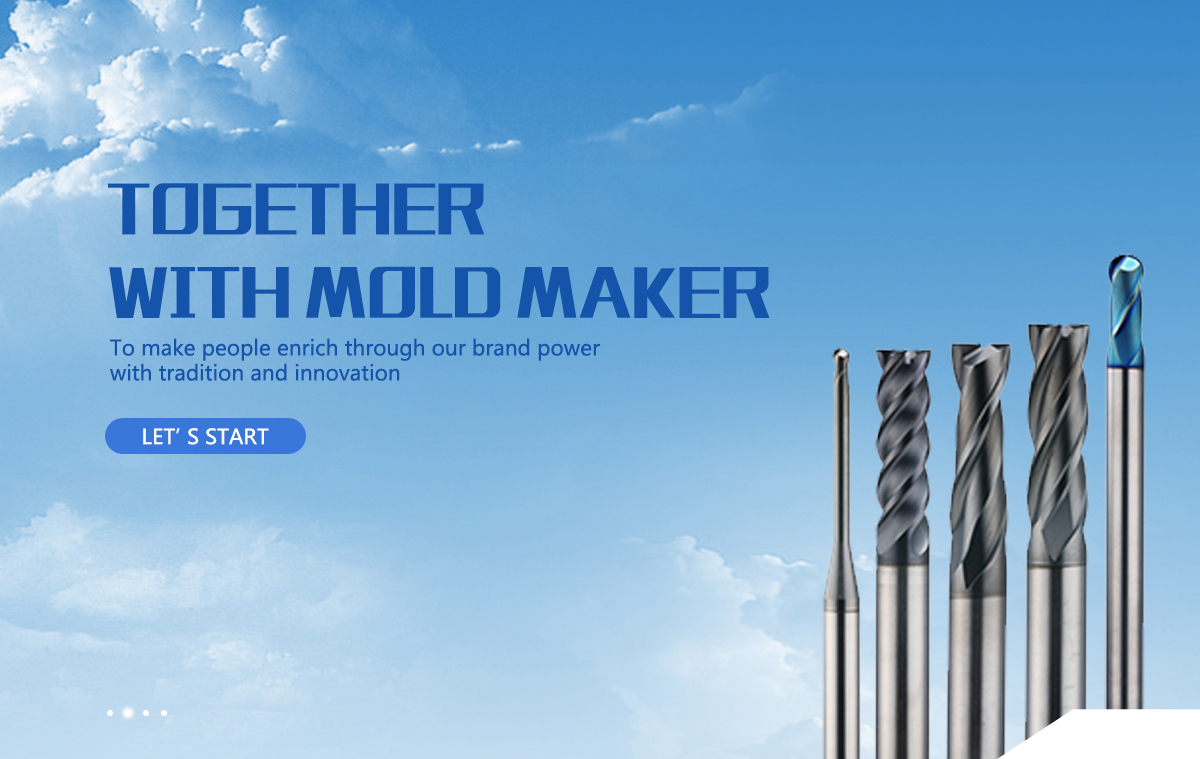
NIKKO KIZAI INC. Page on Alibaba
Together with mold maker
To make people enrich through our brand powe with tradition and innobation.