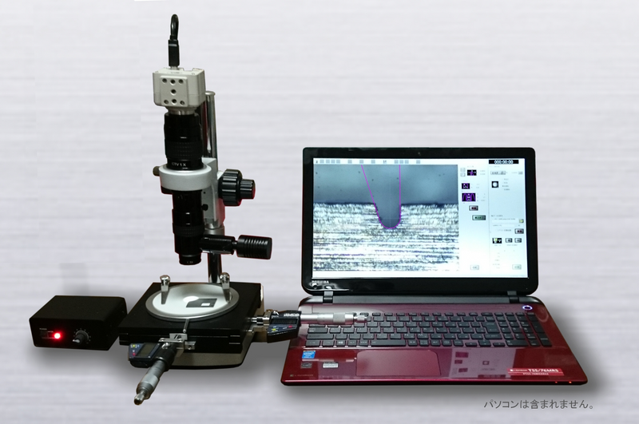
①目的
・プロファイル研削盤の加工量が多く、平面研削盤とプロファイル研削盤で社内の仕事量に差があった。
・NC平面研削盤に一部の加工を対応させ、生産性を高めつつ稼働率を向上させたい。
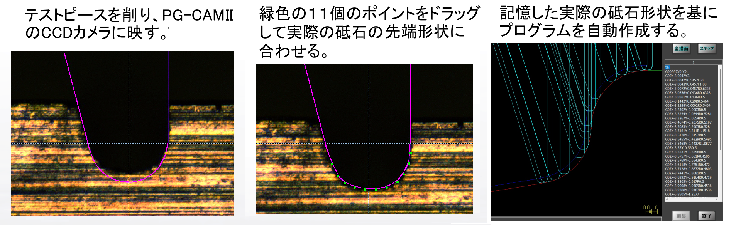
➁導入ポイント
(課題)
NC平面研削盤での形状加工において、形状精度が出ない原因の90%は、砥石の先端形状が摩耗して真円でなくなり、工具径補正が正確に反映されないことによる形状誤差です。形状を正確に把握し、精度向上につなげたい。
(解決策)
NC平面研削盤での加工で0.002mmレベルの加工精度を実現するには、形状精度を左右する要となる砥石先端形状を正確に把握することが必要。
●ポイントナイン PG CAMⅡを使うと…。
・砥石の先端形状を元に目標の形状を加工するための加工プログラムを自動で生成することができる。
・砥石先端の形状を正確に把握できるため、「工具径補正を使うことなく、砥石の実際の先端形状を元に
DXF図形を加工するにはどのように砥石を走らせればよいか」という加工プログラムを自動で作成することができる。
③実例
機上でテストピースを削り、そのテストピースをCCDカメラで映し出して、実際の砥石の先端形状を把握する。その後、当システム専用のCADソフトウェアにて、把握した砥石形状で目標図形を加工するための軌跡(=加工プログラム)を自動で生成し、NC装置に転送して加工を行った。
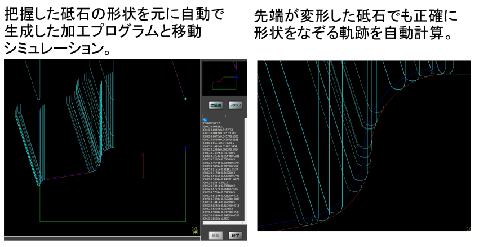
④結果
・平面研削盤での形状加工では0.02~0.04mm程度の加工精度しか出なかったため、
仕上げはプロファイル研削盤で行っていた。当システムを導入したことで、コンスタントに
±0.003mmの精度が得られるようになり、プロファイル研削盤の工程が不要になった。
・±3~5μmの幅でばらついていた形状精度が、デモ加工の時点で一発で±0.002mmの精度が出た。
・プロファイル研削盤に偏っていた工程の分散化ができ、生産性が上がった。
・NC円筒研削盤でもコンスタントに1000分台の精度で形状加工をすることができるようになった。
こんな悩みや課題を抱えている方におすすめ
NC平面研削盤・NC円筒研削盤で容易に加工精度を上げたい。安心して加工したい。
導入すればこんなメリットが期待できる!
- 最短時間で加工精度を上げることができる。
- NC平面研削盤では不可能だと思われていた0.002mmレベルの加工精度の達成。
- 経験の浅いオペレーターでも高精度加工が可能。
- 砥石を加工物にぶつける可能性が激減する。