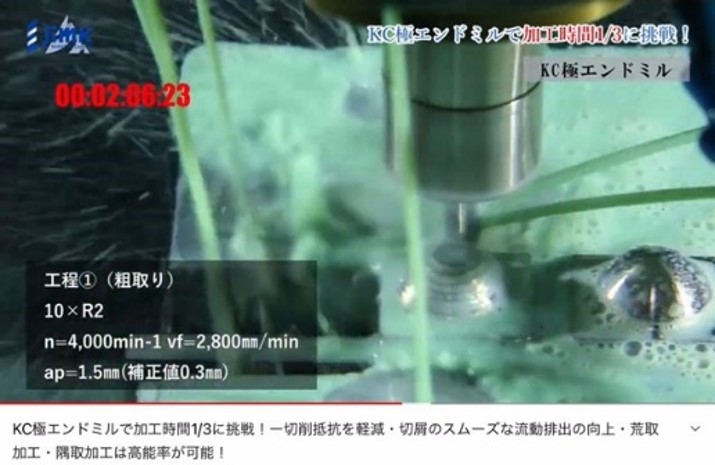
➀ Purpose
By replacing the "three-dimensional contour line shape processing" that was conventionally performed with a carbide ball end mill with a KC radius end mill and processing it, the "effect obtained" is maximized.
(2) Points of introduction
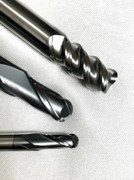
・Significantly shortening
of machining time, reduction
of the type and number of end mills used, concentration of processing processes, improvement
of
accuracy by stabilizing machining and the above merits reduce total machining costs
(3) Processing verification
Scrape the hemispherical shape of R10 from the NAK80 20mmX20mmX10mm workpiece.
The performance of the carbide ball end mill and the KC radius end mill will be compared and the effect will be verified.
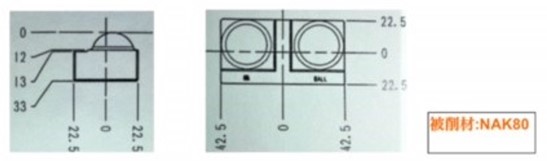
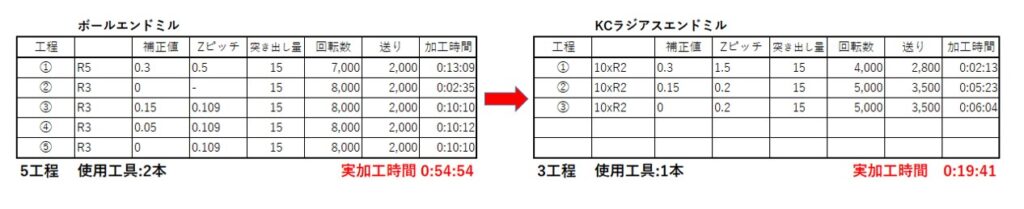
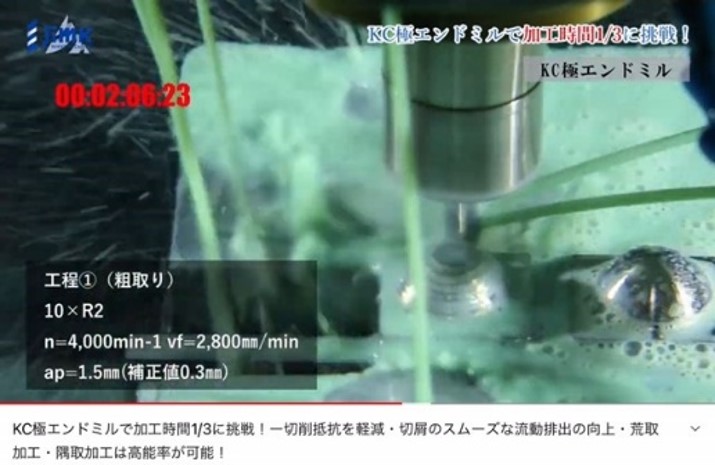
(4) Results
【From roughing to finishing】
Two types of end mills, Carbide Ball End Mill→ R5 and R3, were used Only
one KC Radius end mill →φ10xR2 was supported.
【From roughing to finishing】
5 processes → carbide ball end mill KC Radius end mill →
3 processes and 40% reduction.
【From roughing to finishing】
Processing of carbide ball end mill →total 55 minutes→ The same processing was completed in just under 20 minutes
KC Radius End Mill (Shortened to about 1/3 successful!). )
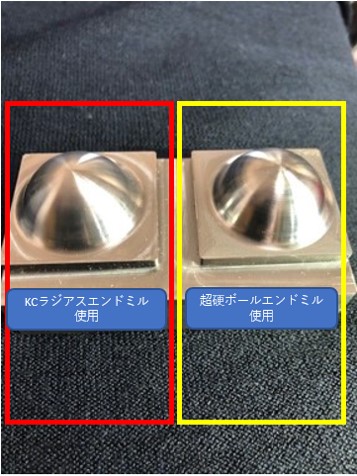
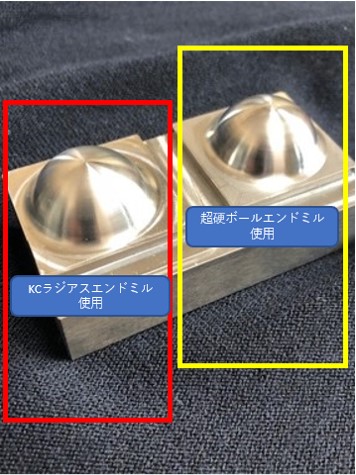