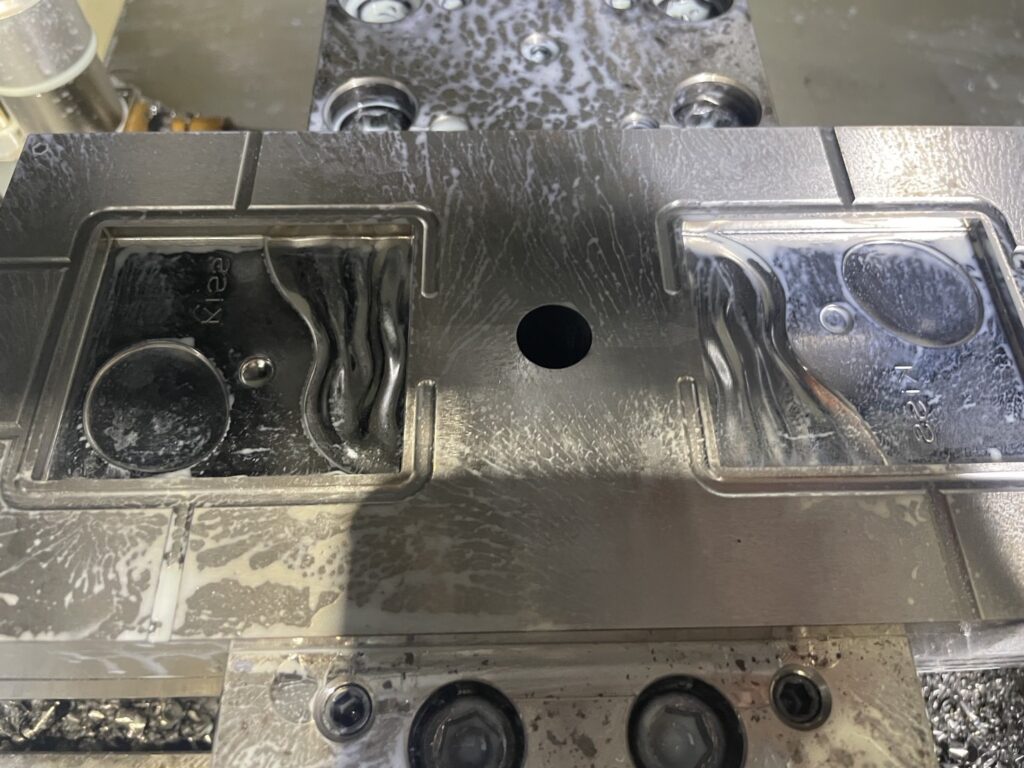
①目的
・従来、ボールエンドミルで行っていた粗加工は安定性が高い一方で、加工時間が長く、工具交換の手間もかかっていた。
・加工効率を向上させるとともに、トータルコストを削減する方法として、ラジアス加工の提案を行った。
②導入ポイント
1, ラジアス加工の優位性を説明
ボールエンドミルと比較し、粗加工から仕上げまで1本で対応可能。
長期的なトータルコスト削減が期待できる。
お客様の実際の加工条件を考慮
2, 試験導入に際して、複数メーカーのラジアスを用意。
比較しやすい環境で加工テストを実施。
具体的な製品提案
3, MOLDINO製のEHHRE-TH3を含めた選定を実施。
③実例
弊社のお取引き先のお客様に、現在使用されているボールエンドミルに代わる工具として
ラジアスエンドミルを用いた加工を提案したところ興味を持たれ、ボールエンドミルとの比較で試験加工を実施。
試験では、2つのメーカー製ラジアスを使用。
今回加工で使用した被削材はNAK-80で実施(形状は複雑で加工精度が求められるもの)。
加工条件は、ボールエンドミルと同様の設定で比較。
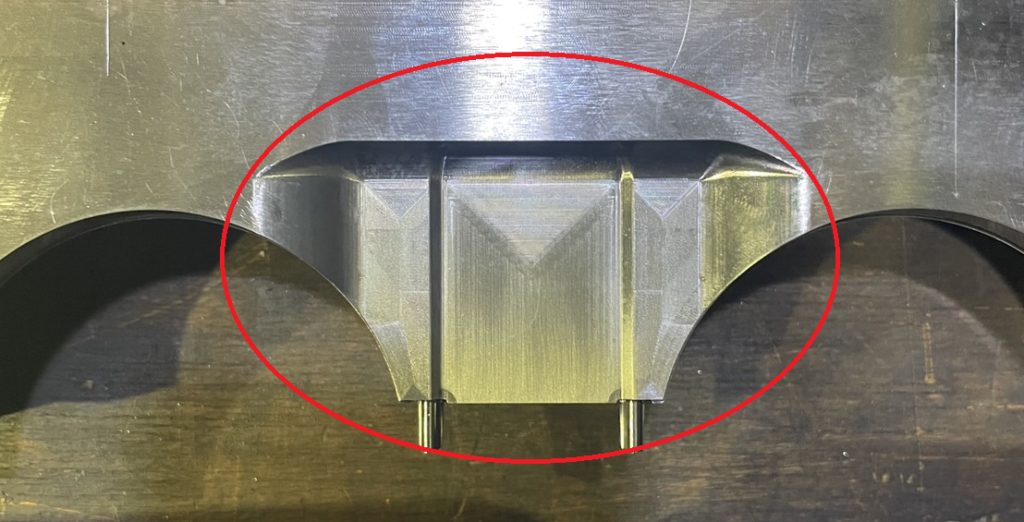
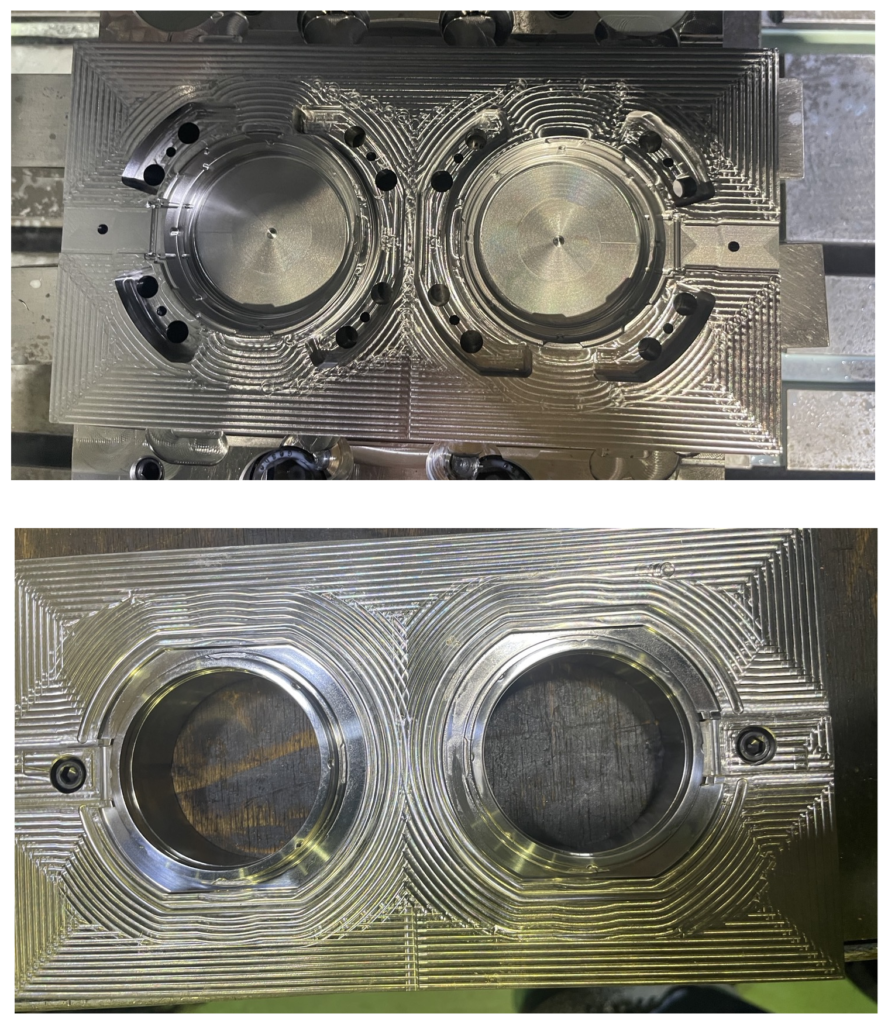
④結果
・加工時間の短縮
MOLDINOのEHHRE-TH3では、他メーカー品に比べて加工時間が半分に短縮。
特に荒加工の加工時間は他社製φ6ラジアスだけで約9時間加工に時間がかかっていたが、
EHHRE-TH3は1本のみで1時間弱で完了することができた。
・効率の向上
粗加工から仕上げまで1本で完結。工具交換の手間が省け、作業効率が向上。
・コスト削減
ラジアスの初期費用はボールと比べて高いものの、加工時間短縮や工具交換の削減による
長期的なトータルコストの低減を実現。
担当営業より
今回の事例では、ラジアス加工の導入により作業効率の向上とコスト削減が実現しました。
これを機に、ラジアス加工への切り替えをお考えの方は、ぜひ当社の営業までご相談ください!